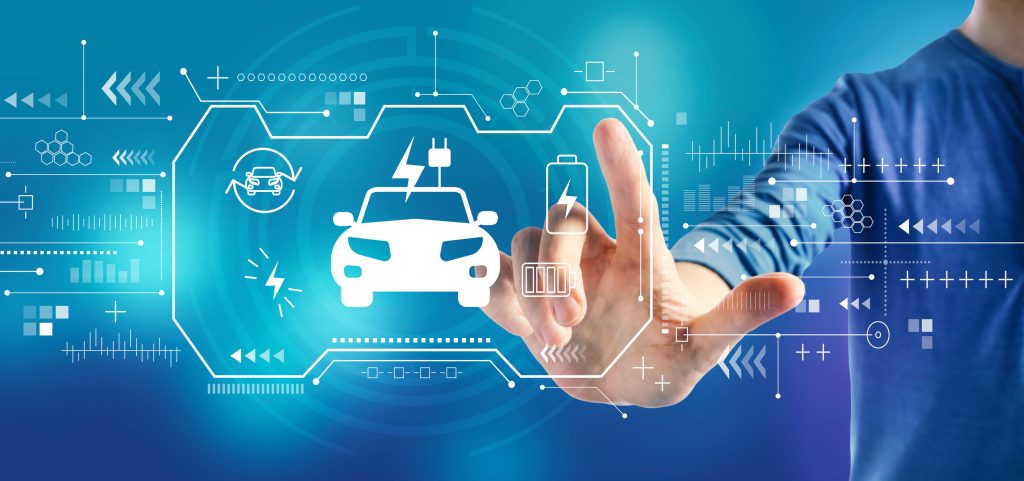
Authors:
Phil Ebbert – VP Engineering at Riedon, Inc.
Krunal Maniar – Business Development Manager at Texas Instruments
To control energy flow and optimize efficiency in high-power industrial systems such as motor drives, uninterruptible power-supplies (UPS), solar inverters, battery systems, etc and automotive systems such as traction inverters in electric vehicles, accurate current measurements at high common-mode voltages are essential.
These high-power systems are subjected to hostile environments such as electrical noise, vibration, mechanical shock, temperature variations, ingress of contaminants. Since these current measurements are measured on the power drive side or called the “hot-side”, the measurements are galvanically isolated and sent across to the micro-controller side or the “cold-side”.
However, new active shunt technology now offers an all-in-one solution that combines highly accurate measurement and isolation in a single package.
Current monitoring applications
Any application that generates or uses significant amounts of electrical power needs to operate as efficiently as possible and, in many cases, this means that there will be some form of automatic closed-loop feedback which requires accurate current sensing.
Large battery systems have become more prevalent in recent years, providing power to essential infrastructures such as data centers and hospitals. Monitoring capacity and usage require accurate current measurement. Motors are being used more than ever to automate our world and as we move towards more efficient BLDC types, current measurement is an essential aspect of electronic commutation.
Many of the high-growth sectors, including renewable energy and xEV require accurate current monitoring for management, reporting, and control.
Methods of current monitoring
There are two primary methods of current monitoring in use for DC; resistive shunt and Hall Effect.
The Hall Effect approach relies on magnetic flux coupling to induce a current into a sensing element. This approach offers inherent isolation.
On the downside, Hall Effect solutions are relatively expensive, especially when high accuracy and high dynamic range is required for renewable energy and xEV applications. Also, they generally have an upper-temperature limit at +85°C which is fairly easy to reach in space-constrained high-power applications.
The shunt approach is relatively simple and involves inserting a low-value resistance in the conductor carrying the current to be measured. The resistance generates a voltage proportional to the current as defined by Ohm’s Law and this voltage is subsequently amplified and monitored to monitor the current.
The main drawback of the shunt approach is that it is an intrusive measurement, and some power is dissipated as heat in the resistance.
Figure 1: Comparison of shunt-based and Hall-based current measurement
There are, however, many positive aspects to shunt-based measurement of current. Firstly, Shunt-based measurements offer higher accuracy and more stability over time and temperature. On most occasions, a one-time initial calibration in production should suffice the long-term accuracy requirements.
One of the greatest strengths of shunt measurements is that they are immune to magnetic fields. In high-power applications, especially motors and xEV, the significant currents flowing in nearby conductors create magnetic fields which can distort readings taken with Hall Effect techniques. Additionally, shunts are able to operate at higher temperatures than Hall Effect devices which is valuable as many power-related applications operate at elevated temperatures.
Active shunt technology
Generally speaking, direct current measurement up to 50A has tended to use shunt-based solutions while higher currents have been measured with the Hall Effect. However, as designers are requiring highly accurate current measurements at high current in a variety of modern applications, the shunt approach is having somewhat of a revival.
A new approach to shunt current measurement combines a traditional passive shunt (resistance) element with an isolated amplifier to produce a solution that incorporates all of the benefits of shunt measurement, along with the isolation from Hall Effect sensing techniques.
The new Riedon Smart Shunt (SSA) integrates an extremely low-value manganin shunt resistor with a high-precision isolated amplifier and an isolated DC/DC converter to provide an active shunt solution. It provides a differential output that can be directly interfaced to most microcontrollers (MCUs). In fact, the SSA is the only amplified, active shunt with an analog output currently available in the market.
Figure 2: The SSA contains an isolated power supply and isolated amplifier as well as the shunt element
The all-in-one solution is extremely easy to design in and install requiring simple bolting to the busbar with all electrical connections (power and signal) being made via a single convenient connector. The SSA is insensitive to magnetic fields, therefore it is able to be positioned freely without any need for additional shielding, unlike Hall Effect solutions, giving system designers greater flexibility.
Capable of measuring currents over 1000A, the SSA offers an accuracy of ±0.1% across the measurement range, with linearity of ±0.1%. Long-term stability is less than 0.2% after 1,000 hours at 45°C, removing the need for annual re-calibration. The differential output effectively negates any thermal EMF effects, eliminating any associated offsets due to a thermal gradient across the device.
Unlike other shunt solutions, the fully UL94-V0 encapsulated device offers reinforced isolation of 1,500VDC (1,000VAC rms) which allows the device to be fitted to the high side in power converters, although fitting to the low side remains recommended as best practice.
As the SSA includes an amplifier, the resistance value is extremely low as the sense voltage is multiplied internally. As a result, power loss when measuring currents up to 1,000A is in the region of 5-20W.
The rugged device includes an automotive-grade, AEC-Q100-certified isolated amplifier from Texas Instruments that supports the ability to operate over the temperature range -40°C to 125°C
While the isolated amplifier inherently provides a differential output that has a number of benefits, if a single-ended signal is required for certain applications then this can be achieved with a simple operational amplifier circuit.
Figure 3: Single-ended conversion requires a simple operational amplifier circuit
The differential output of the isolated amplifier is often converted to a single-ended analog output with an op-amp-based circuit. This op-amp-based circuit can also implement a low-pass filter to further reduce the signal bandwidth to a bandwidth of interest and thereby improve the system noise performance.
Summary
With flexible, accurate, and robust current measurement, it is possible to achieve precise control and so achieve optimum efficiency.
Measuring DC current has been performed in one of two principal ways; a series shunt or Hall Effect probe, each of which have their own advantages and challenges.
However, a new active shunt solution combines the best features of shunt measurement and Hall Effect probes. The convenient single module solution is immune to stray magnetic fields and highly stable over time and temperature, eliminating the need for expensive calibration. It offers the higher accuracies necessary in modern applications as well as being cost-effective and easy to install in busbars or on a panel with the optional isolating adapter.